Plastisol Screen Printing
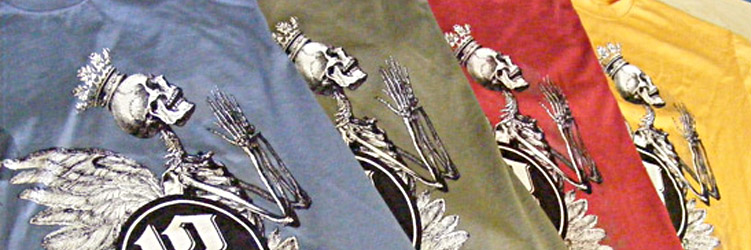
Plastisol ink is a PVC (polyvinyl chloride) based system that essentially contains no solvent at all. Along with UV ink used in graphic screen printing, it is referred to as a 100% solid ink system. Plastisol is a thermoplastic ink in that it is necessary to heat the printed ink film to a temperature high enough to cause the molecules of PVC resin and plasticizer to cross-link and thereby solidify, or cure. The temperature at which most plastisol for textile printing cures at is in the range of 149 °C to 166 °C (300 °F to 330 °F).
Plastisol is the ink of choice for printing of finished goods such as T-shirts, sweatshirts, jackets, and tote bags.
Plastisol can best be described as a “user-friendly” ink because it is very easy to manage. Plastisol can be left in the screen for extended periods of time without clogging the mesh. It is ready to use right out of the container more than 90% of the time. In most applications, it can be printed wet-on-wet, which allows for increased production speeds. It comes in formulations that can be printed on light and dark fabrics. And, in most municipalities, the disposal of waste plastisol is a very simple process.
Plastisol does not “dry”. In order for a compound to dry, there must be evaporation of some kind of solvent. Since plastisol has little or no solvent, it cannot dry. Because of this characteristic, plastisol can be left in screens, the lids can be left off of the ink containers (although keeping them covered is a good practice to keep lint and dirt out of the ink). And ink left at the end of the job can be returned to the container for reuse without any adverse affects. This last practice is a great benefit in reducing waste product.
Plastisol is extremely versatile in that most printers never have to amend the ink. They are able to use it direct from the container without ever adjusting the viscosity or the strength. Plastisol comes in strengths from transparent to very opaque and most printers will have the various versions available to use, depending upon the type and color of fabric they are printing on. The various opacities of ink also vary greatly in price with the most opaque being the most expensive, mainly due to the cost of the increased pigment. So, good shop management dictates that the proper opacity be applied toeach fabric in order to be cost effective.
Plastisol Disadvantages
Since Plastisol is a thermoplastic, it will remelt if it comes in contact with anything hot enough. For that reason, plastisol prints cannot be ironed. If an iron touches a print, it will smear the ink.
Plastisol ink also creates an ink film that can be felt with the hand. The higher the opacity of the ink, the greater the hand. This heavy hand is considered a disadvantage at the consumer level.
One of the most important practices when using plastisol ink is to keep the ink clean. What this statement means, is that it is very beneficial, and cost effective, to keep plastisol colors from being contaminated by dirt, lint, or even other colors of ink. By maintaining clean shop practices, there will be a great reduction in ink waste. Clean ink can be returned to the original ink container for reuse. There is no degradation in the quality of plastisol as long as it is not mixed with other colors or contaminated with foreign materials. Plastisol that has been contaminated with other colors is can still be retained in a separate container for blending with other waste ink. Often times this waste ink can be used to create new colors or, it can be over pigmented with fresh pigment to create a dark color, such as black, for use on less critical jobs. With good plastisol ink management, waste can be reduced to a very small percentage. Plastisol product that is unusable is not considered hazardous waste in most municipalities as long as it is solidified (cured). The best way to achieve this cure is to heat the waste container itself to 160 °C (320 °F) for a period long enough to cure the ink all the way through. In practice, a one gallon container of plastisol will cure all the way through in approximately one hour. If the plastisol needs to be disposed of in an uncured state, then hazardous chemical regulations usually apply. For either cured or uncured disposal, it is recommended that
you always check with local regulatory agencies.
The biggest environmental hazard in the use of plastisol comes in the screen and equipment cleaning steps. In order to emulsify the ink for easy removal from screens, squeegees, flood bars, spatulas, and work surfaces, it is necessary to use some type of solvent. The waste ink and the solvent must be disposed of properly in order to minimize environmental impact. The screen printing industry has been very proactive in the creation of products that can minimize the impact of these cleaning processes. Solvents are available that are “more” environmentally sensitive than the traditional petroleum based solvents. In addition, there are many types of filtration and cleaning systems available to capture inks and solvent residues to minimize the solids that are discharged into the sewer system.